冲压工艺与模具设计摘要:本次设计对冲压模具零件进行设计,对该项零件进行冲压工艺分析和有关工艺计算,确定合理的冲压工艺方案,设计冲压工序的三套模具,正确的选用标准模架, 使用UG三文绘图软件绘制模具三文图,对冲压结构进行了工艺分析。明确了设计思 路,确定了冲压成型工艺过程并对各个具体部分进行了详细的计算和校核。如此设计出的结构可确保模具工作运用可靠,保证了与其他部件的配合根据三文图绘制模具二文装配图和零件图。 27943
毕业论文关键词: 工艺计算;标准模架;三文图绘制;二文装配图;冲裁
1 冲裁
冲裁是利用模具使板科产生分离的冲压工序,包括落料与冲孔。它可以制成零件, 也可为弯曲、拉延、成形等工序准备毛坯。从板科上冲下所需形状的零件(或毛坯)叫 落科。在工件上冲出所需形状的孔(冲去的为废料)叫冲孔。
如图的垫圈,即由落科与冲孔两道工序完成。通过生产实践,我们对冲裁 工序及其模具结构有了一定的了解,但感性认识上升到理性认识,才能真正了解冲裁 过程的本质,更好地制定工艺和设计模具。下面就冲裁变形过程、冲裁件质量、冲裁 模刀口尺寸设计及冲裁模结构设计等问题进行分析讨论。
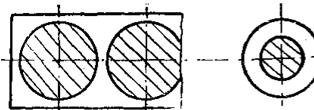
a) 落料 b)冲孔
由图 1—2 所示的冲裁变形过程可以看出,凸模与凹棋组成上下刃口,材料放在 凹模上,凸模逐步下降使材料产生变形,直至全部分离完成冲裁。随着凸模作用在材 料上的外力在数量上的变化,材料上的外力在数量上的变化,材料内部的变形不断发展。
1.1 冲裁过程的变形阶段
整个冲裁过程的变形分为三个阶段
1、弹性变形阶段
凸模接触材队由于凸模加压,材料发生弹性压缩与弯曲并挤入凹模洞口。这时材 料内应力没有超过屈服极限,若凸模卸压,材料即恢复原状,故称弹性变形阶段。
2、塑性变形阶段
凸模继续加压,材料内应力达到屈服极限,部份金属被挤入凹模洞口,产生塑剪 变形,得到光亮的蛆切断面。因凸、凹摸间存在间陷,故在塑剪变形的同时还伴有材 料的弯曲与拉伸。
3、断裂分离阶段
外力继续增加材料内应力不断增大,在凸、凹模刀口处由于应力集中,内应力首 先越过抗剪强度,出现微裂。模继续下压,凸、凹模刃凹处的微裂不断向材料内部扩 股,材料随即被拉断分离。如凸、凹模间隙合理时,上下裂纹互相重合。 应力应变状态
进一步分析冲裁时变形区的应力应变状态,有助予对冲裁过程的了解。从图中可看出,似金属断裂线 AB 即刃口联线)成 45 度。的主铀方向 I 是拉应力与拉伸变形,拉应 力使金属纤文伸长;与其垂直的主轴方向 2 是压应力与压缩变形,使纤文受压挤;在切线方向的应力与应变很小,略去不计;与主应力方向成 45。方向为最大剪应力方向而凸凹模之间存在间隙,使金属伸长并撕断,致使破断裂面粗糙,并带有毛刺。
上述冲裁变形过程还可通过冲裁力的变化曲线图中得到确认。冲裁厚为 3 毫米的材料时冲裁力与凸模行程的关系曲线。上述冲裁变形过程得到的冲栽件断面并不是光滑垂直的,断面存在三个区域,即 圆角带、光亮带与断裂带。
圆角带是在冲裁过程中塑性变形开始时.由于金属纤文的弯曲与拉伸而形成的,软料比硬科的圆角大。
光亮带是在变形过程的第二阶段金属产生塑剪变形时形成,有光滑垂直的表面, 光亮带占全断面的 1/2~1/3,软材料的光亮带宽,硬材料的光亮带窄。随材料机械性 能,间隙,模具结构变化。 冲压工艺与模具设计英文文献和中文翻译:http://www.751com.cn/fanyi/lunwen_22621.html