90年代以来,数控加工技术得到迅速的普及及发展,高速加工中心作为新时代数控机床的代表,已在机床领域广泛使用。自动换刀刀库的发展俨然已超越其为数控加工中心配套的角色,在其特有的技术领域中发展出符合机床高精度、高效率、高可靠度及多任务复合等概念的独特产品。刀库作为加工中心最重要的部分之一,它的发展也直接决定了加工中心的发展。本论文完成的是盘式刀库的总体设计、传动设计、结构设计以及传动部分的运动和动力设计。这种刀库在数控加工中心上应用非常广泛,其换刀过程简单,换刀时间短,定位精度高;总体结构简单、紧凑,动作准确可靠;文护方便,成本低。本刀库减速传动部分分两级减速,一级传动部分采用齿轮减速装置,二级传动部分采用蜗轮蜗杆减速装置,此种设计方案可提高输出轴的传动平稳性能,即提高刀盘的运转平稳性。本刀库满载装刀16把,采用单环排列方式排放,按就近选刀原则选刀。35317
加工中心上普遍采用的刀库是盘式刀库和链式刀库。密集型的固定刀库目前于用于FMS中的集中供刀系统。
盘式刀库 盘式刀库结构简单,应用较多,如图1-4所示。由于刀具环形排列,空间利用率低。因此出现了将刀具在盘中采用双环或多环排列,以增加空间的利用率。但这样一来使刀库的外径过大,转动惯量也很大,选刀时间也较长。因此,盘式刀库一般适用于刀具容量较少的刀库。论文网
1956年日本富士通研究成功数控转塔式冲床,美国IBM公司同期也研制成功了“APT”(刀具过程控制装置)。1958年美国K&T公司研制出带ATC(自动刀具交换装置)的加工中心。1967年出现了FMS(柔性制造系统)。1978年以后,加工中心迅速发展,带有ATC装置,可实现多种工序加工的机床,步入了机床发展的黄金时代。1983年国际标准化组织制定了数控刀具锥柄的国际标准,自动换刀系统便形成了统一的结构模式。
目前国内外数控机床自动换刀系统中,刀具、辅具多采用锥柄结构,刀柄与机床主轴的联结、刀具的夹紧放松机构及驱动方式几乎都采用同一种结构模式。在这种模式中,机床主轴常采用空心的带有长拉杆、碟形弹簧组的结构形式,由液压或气动装置提供动力,实现夹紧放松刀柄的动作。利用这种机构夹持刀具进行数控加工的最大问题是,它不能同时获得高的夹持刚度和刀具振摆精度,而且主轴结构复杂,主轴轴向尺寸过大,加上它的液压驱动装置及刀具辅具锥柄的制造成本,使得自动换刀系统的造价在机床整机中占有较大的比重。
2 文献综述
3 拟解决的关键问题及难点
1.盘式刀库运动由伺服电机驱动,如何做到刀具运输平稳,定位准确?
2.如何是整个设计的运动部分结构简单,重量轻,且具有减小反转间隙的结构?
3.如何选用合适的刀具编码方式,用机械手实现自动换刀?
4 方案论证(包括技术路线和图表等)
刀库的主要参数的确定
载刀容量:16把;
排列方式:单环排列;
刀库半径:300mm;
刀具最大重量:8kg;
盘式刀库刀套线速度:22-35m/min ;
刀库结构示意图如下:
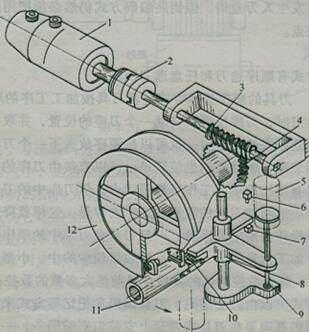
刀库结构示意图
1—电动机 2—联轴器 3—蜗杆 4—蜗轮 5—液压缸 6、7—行程开关
8—拨叉 9—挡标 10—滚子 11—刀套 12—刀盘 数控加工中心盘式刀库设计开题报告:http://www.751com.cn/kaiti/lunwen_33198.html